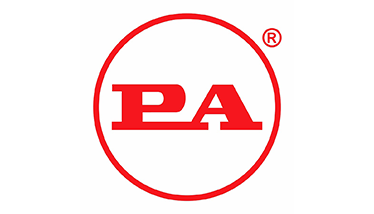
P.A.
P.A. has opted for Microsoft Dynamics 365 Business Central, implemented by EOS Solutions along with specific Logistics, Finance and Sales Apps, to manage a combined planning for different businesses.
About us
P.A. has been operating in the high-pressure washing industry since 1982, producing accessories and equipment for pressure washers, car washing systems and industrial washing. With more than 200 employees and exports representing more than 85 percent of total production, the company has an annual turnover of more than 50 million euros.
Industrial washing within the sectors of: Engineering; Construction; Food; Pharmaceutical
+ 200 employees
Export: 85% of manufacturing
50 M € of turnover
100 % made in Italy
Requirements
We needed a large-scale integration process that would maintain the distinctive features of our business management at the same time.
P.A. asked EOS Solutions for a solution that would integrate all group companies, particularly the local company in the U.S., PA NORTH AMERICA, into a single system, combining different taxation and organizational models.
Such as the in-door management of the production cycle, the centralized production planning, the management of customers shared by PA and PA NORTH AMERICA, and the traceability among all the group's companies.
The Solution
To meet these needs, EOS Solutions chose Microsoft Dynamics 365 Business Central integrating the ERP with an already existing production scheduler to manage a combined scheduling of the different companies.
The project was then completed with specific EOS Apps for Logistics, Finance and Sales that enable to manage load units to be assigned to documents, calculate transportation costs and fees, control cost centers and assign workflows, perform quality audits and digitize factory operations, easily and securely manage documentation, and to analyze data.
Client Information
- Industry
- Industrial washing
Benefits
The most significant change is the possibility of managing all the subsidiaries and participated companies directly from the headquarter. But allowing each company to maintain its own fiscal entity while also expecting even the most complex processes. Such as participating in the cash flow of a subsidiary company, either as a third party or as a supplier.
On the operative side, integrating traceability into the ERP allows us to increase the quality of the production process and provide timely reports on the delivered product. A strategic service, for example for customers in the food and pharmaceutical industries.
Thanks to the ERP's interface with our vertical warehouse, picking and storage operations have also been fully automated, also according to many changes and exceptions.
Finally, the possibility of attaching technical documents, images and other multimedia content to almost all management systems and the ability to export data to Excel for customized data analysis make the new system an extremely effective and versatile management tool even for the new U.S. company.